CFL or compact fluorescent lamp light bulbs are pretty typical these days. A CFL bulb is made up of a ballast and a tube containing gas. The ballast turns the current from the wall outlet into high frequency current, which it sends into the gas tube. The high frequency current knocks excites electrons in the gas, causing them to produce ultraviolet (UV) light. When the UV light hits the fluorescent coating on the glass tube it produces visible light.
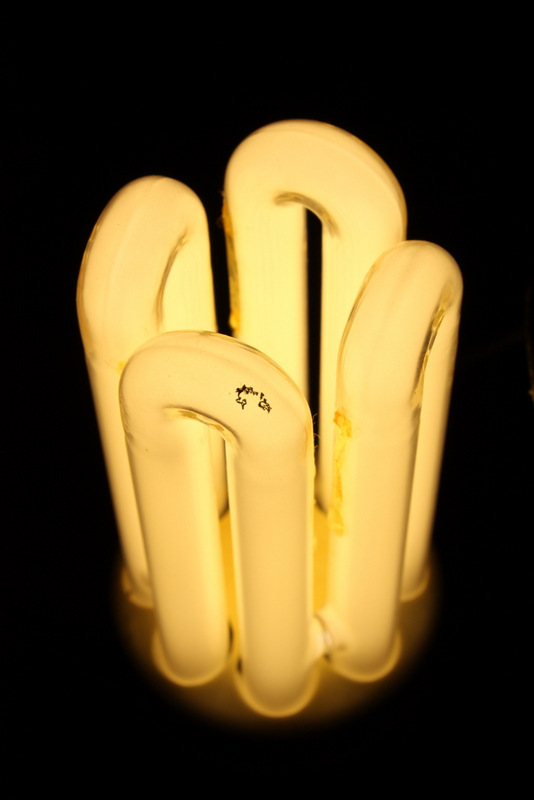
Let’s compare CFL light bulbs directly to the pro and con list I put together last week about incandescent bulbs:
- Light Quality: Mixed Reviews. The light quality can be all over the board with different brands of CFL light bulbs. We’ve grown accustomed to the warm, soft light produced by incandescent bulbs, and in comparison, some brands of CFL bulbs can produce cold, harsh light. However, many brands have improved their designs to provide warm light just like incandescent bulbs. You may have to shop around a couple brands to find the light quality that meets your expectations.
- Price per bulb: Pro. While more expensive than filament bulbs, you can pick up CFL bulbs for around $2 per bulb.
- Availability: Pro. You can get basic CFL bulbs pretty much everywhere you can get filament bulbs these days.
- Style: Con. While CFLs fit pretty much any standard light bulb socket, you’ll have trouble finding specialty shaped bulbs of the CFL variety.
- Energy use: Pro. A CFL bulb that produces a comparable amount of lumens as a 60 watt filament bulb requires only 14 watts.
- Lifetime: Pro. 8000 hours! Which translates into about 7 years of burning for 3 hours a day.
And one more important point to consider when using CFL bulbs:
- Toxicity and Disposal: Con. The gas inside the CFL tube contains mercury which is hazardous to come in contact with. This means you have to be careful not to break open the tube, and you really should not just be disposing of a CFL bulb in the trash. Used CFL bulbs should be disposed of by bringing them to an appropriate drop site for safe disposal.
If you’re looking for a disposal site near you, you can check out search.Earth911.com
So the tally when comparing CFLs to Incandescents is 4 pros, 2 cons, and 1 mixed review. Now let’s look at the long term cost.
10 year cost for burning filament bulbs in one lamp: (3 hours a day, $0.12/kwh cost of electricity, $2.00/bulb, 2 bulbs) = $22.40.
Pretty cheap when compared to the $96.84 it would cost to run the same light with a incandescent bulb.